

University of Arizona Opto-Mechanical Papers Reference. and the stiffness S is fixed by the design, show that the best material is one with a high. To reduce thermal effects, a good match of coefficient of thermal expansion (CTE) of optics and flexure material is helpful. Most high-strength materials have low fracture toughness. "Flexure Mounts for High Resolution Optical Elements" (PPT). Flexure toughness determines its resistance to fracture or cracking.
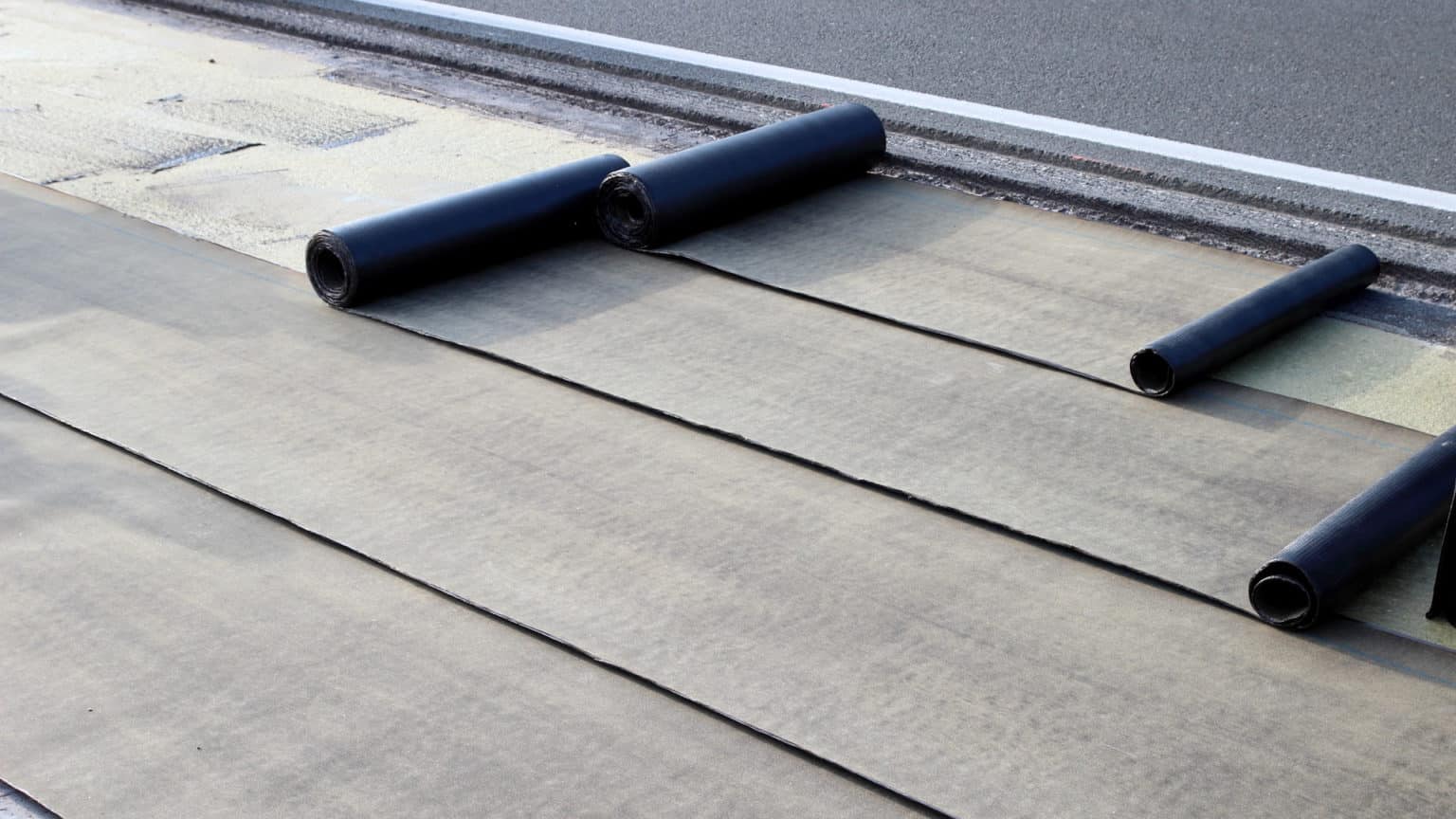
University of Arizona Opto-Mechanical Papers Reference. "Application of Flexure Structures to Active and Adaptive Opto-Mechanical Mechanisms" (PDF). "Three-degree-of-freedom flexure-based manipulator for high-resolution spatial micromanipulation". : Cite journal requires |journal= ( help) "Eliminating Underconstraint in Double Parallelogram Flexure Mechanisms". Additionally, special care must be taken to design the flexure to avoid material yielding or fatigue, both of which are potential failure modes in a flexure design. This makes flexures a critical design feature used in optical instrumentation such as interferometers.ĭue to their mode of action, flexures are used for limited range motions and cannot replace long-travel or continuous-rotation adjustments. or a cementitious material content may be selected from past experience to obtain. Flexures are able to achieve much lower resolution limits (in some cases measured in the nanometer scale), because they depend on bending and/or torsion of flexible elements, rather than surface interaction of many parts (as with a ball bearing). However, the best correlation for specific materials is obtained by. Additionally, conventional bearings or linear slides often exhibit positioning hysteresis due to backlash and friction. High precision alignment tasks might not be possible when friction or stiction are present. In the field of precision engineering (especially high-precision motion control), flexures have several key advantages. And it was found out that Beryllium Copper is the best suitable alloy present for flexure bearing. Using compound flexures, complex motion profiles with specific degrees of freedom and relatively long travel distances are possible. The various analyses of physical and mechanical properties of 1. Dont forget that the grain structure of the material will. Since single flexure features are limited both in travel capability and degrees of freedom available, compound flexure systems are designed using combinations of these component features. My recommendation therefore is to bend in T4 condition and then heat treat to T6 if this is possible.
